October 19, 2023 @ 9:00 am – October 21, 2023 @ 5:00 pm
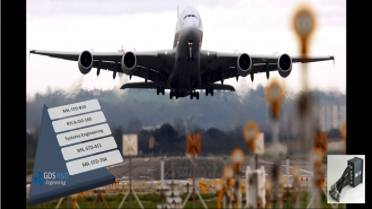
Training on MIL-STD-810H Environmental Testing
with Tailoring Examples
A Hands-on “Online” or “Onsite” Training Class
Led by a live, U.S. based instructor
MIL-STD-810H
US Department Of Defence Test Method Standard
Environmental Engineering Considerations and Laboratory Tests
GDS Engineering R&D, Inc. provides online international training on MIL-STD-810H Environmental qualification testing of military equipment. Training focuses on the standard with tailoring examples. This training is an important step for testing and certifying your military equipment and products in accordance with MIL-STD-810H, platform test requirements, and other applicable standards and specifications.
This page describes the contents of this two and half days of short training.program.You can also download the PDF file that describes the MIL-STD-810H training program. Click here to download the MIL-STD-810H Training Program Description Document. Dr Cicek is the main instructor of this training. Click here to read his bio page.
Training Scope and Contents
- A good understanding of product testing in view of MIL-STD-810G/H and other relevant military standards.
- Overview of Systems Engineering, V&V, and Concepts of Operations (CONOPS) document.
- Establishment of Test Requirements and Test Plans.
- Test Procedures, Scheduling, Implementation, and Test Reports.
- Tests are covered in detail per MIL-STD-810. Altitude, temperature, humidity, shock, vibration, acceleration, salt fog, explosive atmosphere, etc..
- Some of the MIL-STD-810H test methods are covered briefly; however, we ensure all questions are answered for each test method.
- Cases studies, sample reports and discussions on issues.
- Design issues and test failure discussions.
- Risk management for test results and acceptance criteria.
- Design Recommendations.
Platform and equipment test examples are provided in each test method presentations and discussions, including:
- Military aircraft platforms (fixed and rotary wing), ground vehicles, and navy ships
- Avionics, electrical and mechanical systems, and structural project applications
- Test tailoring examples to include the selection of tests, parameter levels, and durations
- Concepts of Operations (CONOPS) document and test curve establishment.
- Tailoring and Life Cycle Environmental Profile (LCEP)
- Mission Profile
- For tailoring, read more at https://www.globaldynamicsystems.com/posts/mil-std-810h-training-tailoring-is-essential-explained/
Training Schedule and Execution Type
- Training Type: International / Online
- Satus: Seats are avaiable now.
- Online training using ZOOM.
- Led by a live, U.S. based instructor (Dr Ismail Cicek) (PDF) (Download PDF)
- A usual 2.5 days of training schedule is as follows:
-
- 1st Day: 09:00 – 13:00
- 2nd Day: 09:00 – 17:00 (Lunch Break between 12:30 and 13:30)
- 3rd Day: 09:00 – 17:00 (Lunch Break between 12:30 and 13:30)
- Time zone: Central Daylight Time (US CDT, UTC-5)
-
- Ending time may vary+/-30 minutes depending on the length of the discussions.
- Course Material: English
- Comm. Language: English
- Material: Registration includes all presentations and additional material (English) shared before the class.
- Attandance: The link for online class is distributed to registered trainees upon registration.
- Attendees will receive a Training Certificate.
- Training includes knowledge check quizzes, a competition type fun way or learning.
Registration Process
To register for a course, do the following:
Individual/Group Registrations:
Training class size is limited with 12 attendees. Please ensure to reserve your seat with the following actions:
1. Review the Training Calendar and select the suitable training for you or for your organization.
2. Fill out the Training Registration Request Form, below this page. We will send you the registration package, via email, including:
- Registration form.
- Daily Training Plan with Sessions and Allocations to Each Subject
- Information about the Payment Process and Account Numbers
- Information about the Class Material Link
- Information about the Training Attandance Link
Organizational (Closed) Trainings:
Please fill out the Training Registration Request Form, below this page. Ensure to describe
- The number of your personnel that will be planned for attandance (approximately)
- Preferred month (please mention with flexible dates) of the training to be scheduled.
- If there are any, please specify the subjects or application interests to emphesize in the training contents.
About the Instructors
The main instructor of the training is Dr Ismail Cicek. An Avionics Chief Engineer (EE) who is also a Certified Verification Engineer (FAA/EASA) also assists the trainings. Our experienced test personnel also becomes avialable for demonstrations and discussions.
A Certified Verification Engineer (CVE) iaw FAA/EASA and with 18 years of experience. He has worked as the avionics systems chief engineer in product development of avionics systems. He is also experienced in the product testing per environmental and EMI/EMC standards and FAA/EASA certification processes.
Our experienced personnel also support our training programs. They are actively participating in the environmental testing of products.
Dr. Ismail Cicek studied PhD in Mechanical Engineering Department at Texas Tech University in Texas, USA. He study included random vibration. He has both industrial and academic experience for over 30 years.
He gained engineering and leadership experience by working in the United States Department of Defence projects and programs as systems development engineer for 15 years. He led the development of various engineering systems for platforms including C-5, C-17, KC-10, KC-135, and C-130 E/H/J. Dr. Cicek’s experience includes unmanned aerial vehicle development where he utilized the Geographical Information Systems (GIS) and Malfunction Data Recorder Analysis Recorder System (MADARS) development for military transport aircraft.
Dr Cicek worked as the lab chief engineer for five years at the US Air Force Aeromedical Test Lab at WPAFB, OH. He received many important awards at the positions he served, due to the excellent team-work and his detail oriented and energetic personality. These included Terra Health’s Superior Client Award in 2009 and Engineering Excellence Award in 2010 as well as an appreciation letter from the US Air Force Aeronautical Systems Center (ASC), signed by the commander in charge.
Dr Cicek also established a test lab, called Marine Equipment Test Center (METC) and located at Istanbul Technical University, Tuzla Campus, for testing of equipment per military and civilian standards, such as RTCA-DO-160. Providing engineering, consultancy, and training services to many companies and organizations, Dr. Cicek has gained a great insight into the tailoring of standard test methods in accordance with military standards, guides, and handbooks as well as Life Cycle Environmental Profile LCEP) developed for the equipment under test.
Dr. Cicek also completed various product and research projects, funded in the USA, EU, and Turkey. He is currently teaching at Istanbul Technical University Maritime Faculty, Tuzla/Istanbul. He is the founding manager of the METC in Tuzla Campus of ITU. Meanwhile, he provided engineering services, consultancies, and training to many organizations for product development, engineering research studies such a algorith development, test requirements development, and test plans and executions.
Dr Cicek worked as the Principle Investigator and became a Subject Matter Expert (SME) at the US Air Force Aeromedical Test Lab (WPAFB/OH) for certifying the products to the US Air Force Platform Requirements. He also developed Joint Enroute Care Equipment Test Standard (JECETS) in close work with US Army Test Lab engineers and managers.
Read DAU Paper: “A New Process for the Acceleration Test and Evaluation of Aeromedical Equipment for U.S. Air Force Safe-To-Fly Certification”. Click to display this report.
Connect with Dr Ismail Cicek: Linkedin Page
Click here to read more about Dr Cicek’s professional studies.