Hermetically Sealed Equipment technology refers to the sealing methods used in the manufacture of electronic, mechanical, and optical components that effectively prevent the ingress of air and water. The term "Hermetic" is derived from the Greek myth of Hermes. It emphasizes the sealing of these components against the environment.
Hermetically sealed equipment test is tested up to what pressure levels?
Hermetically sealed equipment is typically tested to pressure levels that are higher than their intended operating pressures to ensure their integrity and ability to withstand potential stresses. The specific pressure levels used for testing can vary depending on several factors, including:
Industry standards and regulations: Different industries and applications may have specific standards or regulations that dictate the required pressure levels for hermetic seal testing. For example, the aerospace industry may have more stringent requirements compared to consumer electronics.
Design and intended use: The design of the equipment and its intended use also play a role in determining the test pressure levels. Equipment designed for harsh environments or critical applications may be subjected to higher test pressures.
Type of seal: The type of hermetic seal used can also influence the test pressure. Different seal materials and designs have different pressure tolerances.
While the exact pressure levels can vary, here are some general guidelines:
- Gross leak testing: This test is used to detect large leaks and is typically performed at pressures ranging from 1 to 5 psi (pounds per square inch) or higher.
- Fine leak testing: This test is used to detect smaller leaks and is typically performed at pressures ranging from 15 to 30 psi or higher.
- Pressure decay testing: This test measures the rate of pressure decay over time and is typically performed at pressures ranging from 30 to 100 psi or higher.
- Proof pressure test: This verifies the structural integrity of the equipment by subjecting it to a high pressure for a specific time.
Common Testing Pressure Levels:
- Refrigeration and HVAC systems:
- Typically tested at 1.1 to 1.5 times the maximum operating pressure.
- For example, a system with a maximum operating pressure of 300 psi might be tested up to 450 psi.
- Industrial or process equipment:
- Often subjected to hydrostatic or pneumatic pressure tests at levels specified in design codes such as ASME Boiler and Pressure Vessel Code.
- Test pressures are generally 1.25 to 1.5 times the design pressure.
- Electrical or electronic hermetically sealed devices:
- May undergo leak testing using helium or other gases at pressures ranging from a few psi to 500 psi, depending on the sensitivity of the equipment.
Specific Standards and Regulations on the Hermetically Sealed Equipment
To find the exact pressure level for a specific piece of equipment, you'd need to consult its design specifications, relevant industry standards (like MIL-STD-883 for microelectronics), or the manufacturer's documentation. Generally, these tests are conducted according to relevant standards such as ASHRAE, ANSI, ISO, or UL, depending on the industry. Some examples of standards and regulations that specify pressure levels for hermetic seal testing include:
- MIL-STD-883: This military standard is widely used for microelectronic devices and includes test methods for hermetic seals.
- MIL-STD-202: This military standard covers various environmental tests for electronic and electrical component parts, including hermetic seal tests.
- ASTM F2391: This ASTM standard specifies test methods for measuring the hermeticity of electron devices using helium as a tracer gas.
- UL 1995 for HVAC systems specifies certain test pressures for hermetically sealed components.
- ISO 19900 (general industrial standards) may require pressure tests at specific multipliers of operating conditions.
It's important to consult the relevant standards and regulations for your specific application to determine the appropriate pressure levels for hermetic seal testing.
What type of equipment, devices or parts can be hermetically sealed equipment?
Hermetically sealed equipment, devices, or parts are designed to prevent the ingress or egress of air, moisture, or other contaminants. This ensures the internal environment remains protected and isolated from external conditions. Such sealing is commonly used in various industries, including electronics, medical, refrigeration, aerospace, and more. Below are examples of equipment, devices, and parts that can be hermetically sealed:
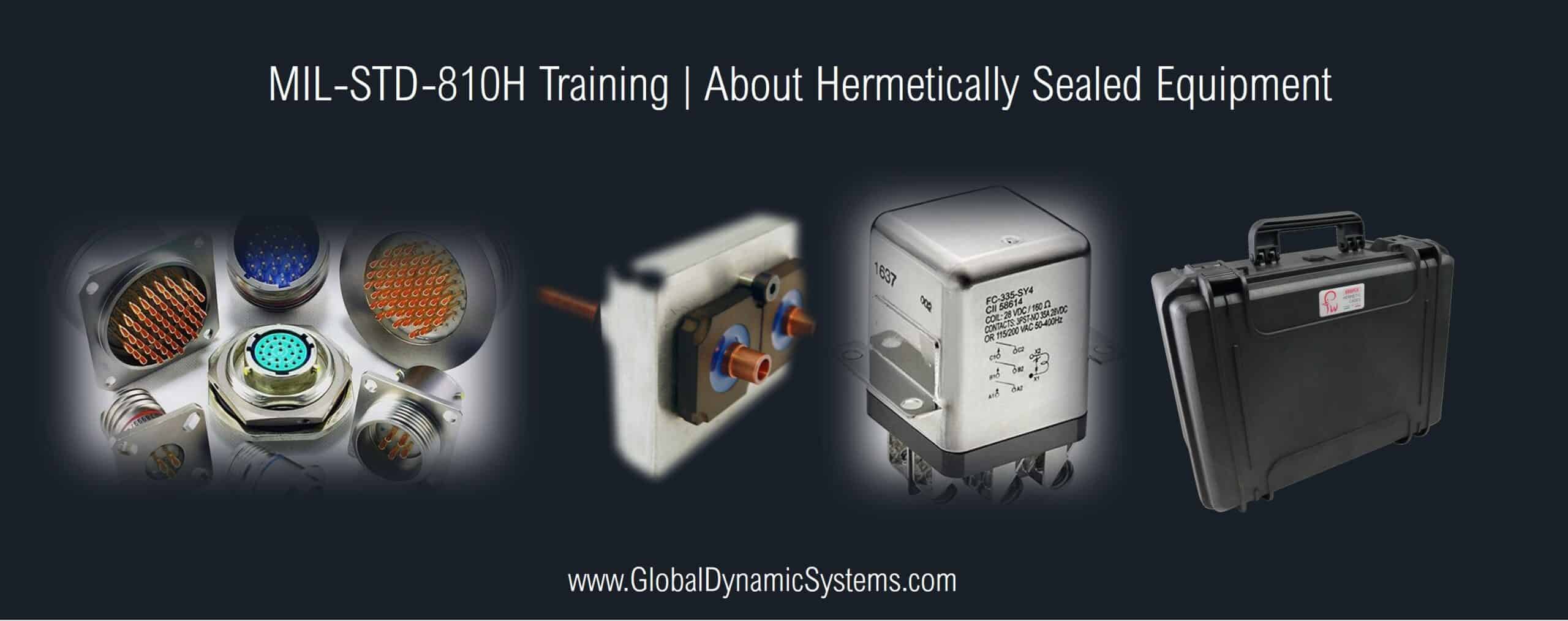
Below are examples of equipment, devices, and parts that can be hermetically sealed:
1. Electronics and Semiconductor Components
- Integrated Circuits (ICs): Sealed to protect delicate microelectronics from moisture and contaminants.
- Sensors: Pressure, temperature, and other sensors used in harsh environments.
- Vacuum Tubes: Used in older electronics or specialized applications like high-frequency devices.
- Quartz Crystals and Oscillators: Used in time-keeping and signal-processing applications.
- MEMS (Microelectromechanical Systems): Such as accelerometers and gyroscopes.
2. Medical and Laboratory Equipment
- Pacemakers and Implantable Devices: Protecting electronics from bodily fluids.
- Sterile Medical Instruments: For maintaining cleanliness and sterility.
- Blood Gas Analyzers: Sealed to maintain accurate gas measurements.
- Medical Packaging: Containers for storing sterile medications or instruments.
3. Refrigeration and HVAC Components
- Compressors: Used in refrigerators, air conditioners, and industrial cooling systems to prevent refrigerant leakage.
- Expansion Valves: To ensure accurate refrigerant flow without contamination.
- Refrigerant Lines and Seals: For preventing leaks in cooling systems.
4. Aerospace and Defense Equipment
- Avionics: Sealed components to function reliably at high altitudes and in extreme temperatures.
- Optical Sensors: Used in satellites or military applications.
- Missile Guidance Systems: To ensure reliability in harsh conditions.
- Batteries: Protected from atmospheric pressure changes.
5. Industrial and Process Equipment
- Vacuum Pumps: Designed to maintain low-pressure environments.
- Switchgear and Relays: To prevent electrical arcing and protect internal mechanisms.
- Pressure Transducers: Used in industrial monitoring systems.
6. Automotive Parts
- Fuel Pumps and Injectors: Protected from fuel contamination.
- Electronic Control Units (ECUs): Sealed to prevent water and dirt ingress.
- Airbag Sensors: To ensure reliability in all conditions.
7. Optical and Communication Devices
- Fiber Optic Connectors: To prevent light loss or contamination.
- Cameras: Used in underwater or harsh environments.
- Sealed Lenses: To protect sensitive optical components.
8. Batteries and Energy Storage
- Lithium-Ion Batteries: Sealed to prevent chemical exposure.
- Energy Cells in Space Applications: To function in a vacuum or radiation-heavy environments.
9. Military and Harsh-Environment Equipment
- Explosives and Detonators: Sealed for safety and reliability.
- Submarine Electronics: For operation under high-pressure conditions.
- Radars and Communication Equipment: To prevent malfunction due to environmental exposure.
10. Packaging and Storage Containers
- Hermetically Sealed Food Containers: For long-term preservation.
- Pharmaceutical Packaging: Ensuring sterility and extended shelf life.
- Ammunition Cases: To prevent corrosion and degradation.
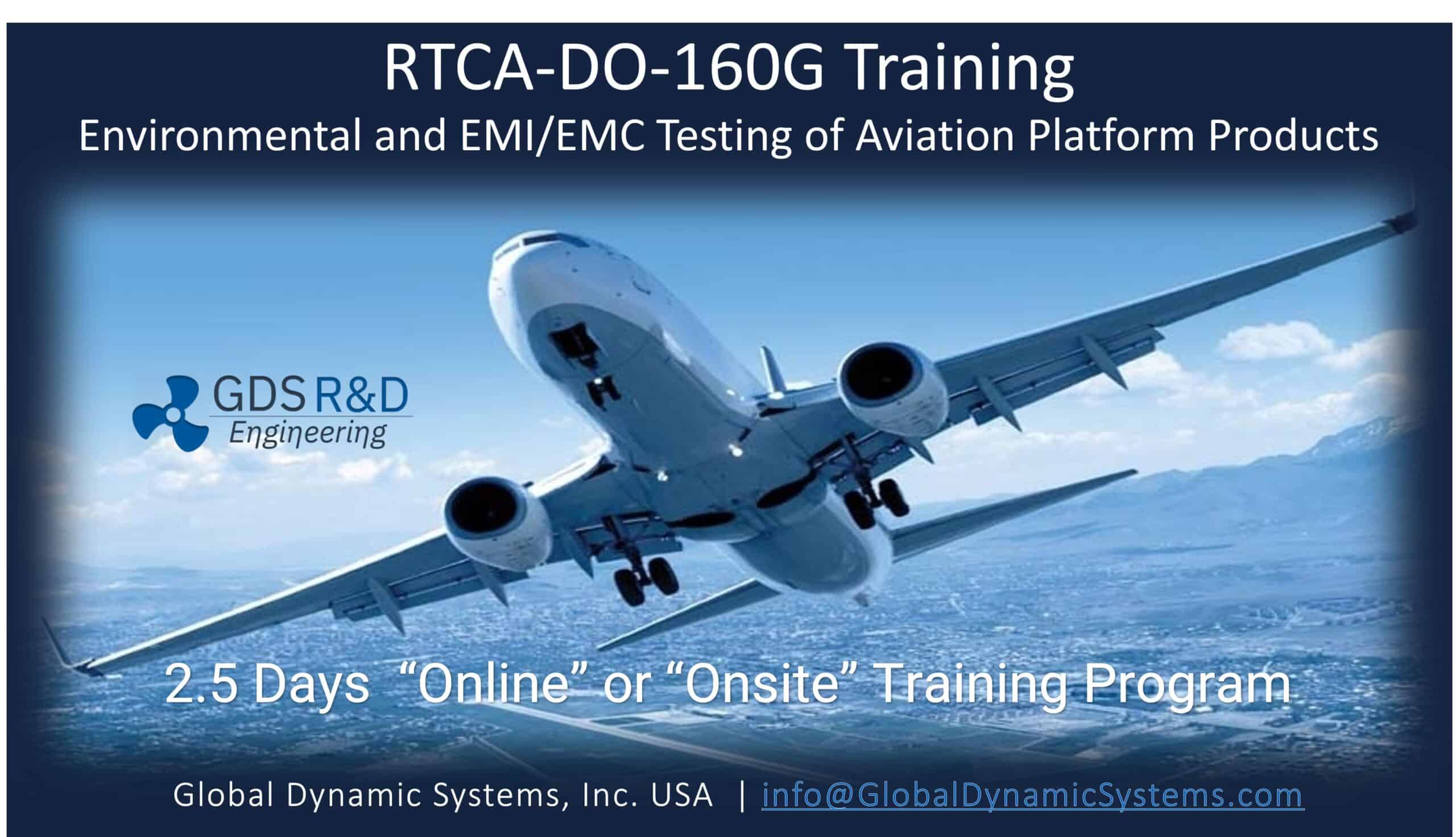
RTCA-DO-160G Training
We provide training on the RTCA-DO-160G testing and we include the design tips such as found on this web page.
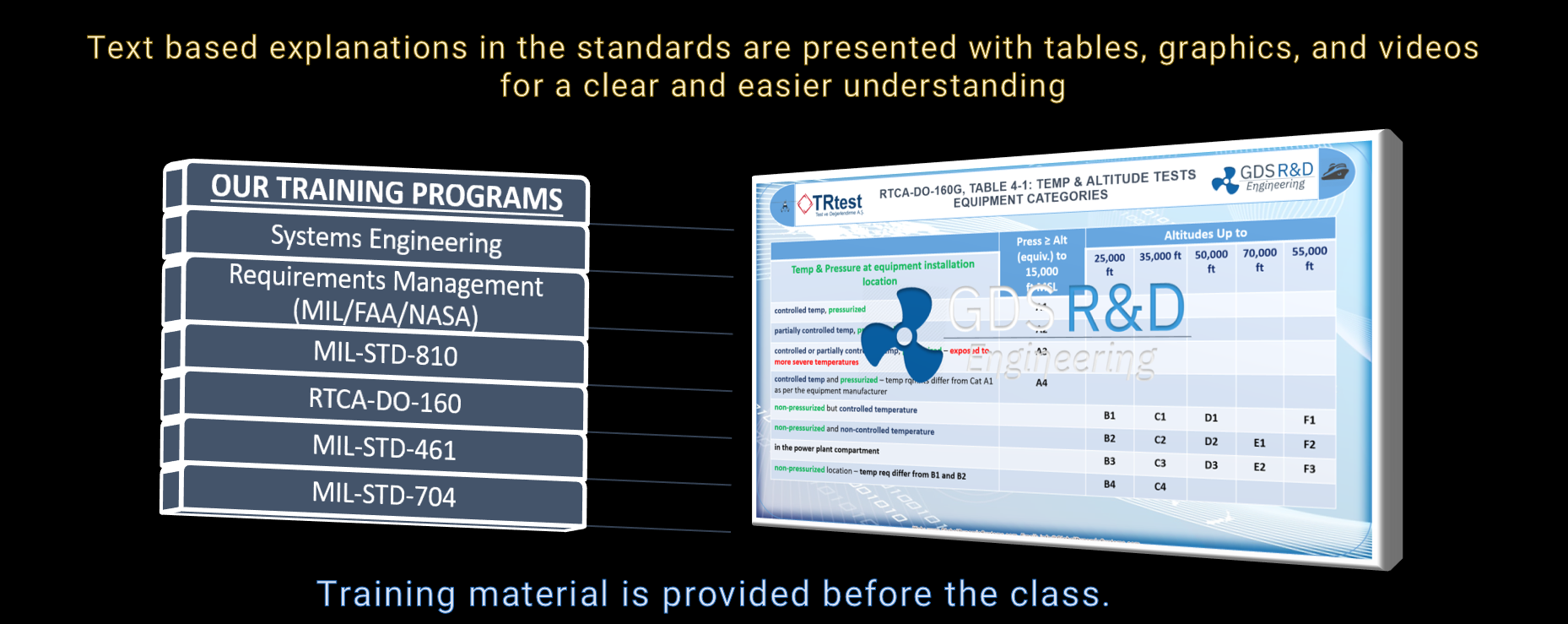
MIL-STD-810H Training
We provide training on the MIL-STD-810H testing and we include the design tips such as found on this web page during the training with enough coverage and examples for your applications.
Hermetically Sealed Equipment Testing in accordance with MIL-STD-202
Test Method 112 - Seal (Hermeticity) Test:
This test evaluates the hermetic seal of a component, ensuring it prevents moisture or gases from entering.
General Procedure:
- Preparation: Clean the component to remove any contaminants.
- Tracer Gas Introduction:
- The internal cavity may be pressurized with a tracer gas, such as helium.
- Leak Detection:
- Use a mass spectrometer or other detection methods to measure the leakage rate of the gas escaping the sealed component.
- Leak Rate Measurement:
- The acceptable leak rate is defined by the specification for the component type.
- Leak rates are often expressed in terms of atm·cc/s (atmosphere-cubic centimeters per second).
Test Types:
- Fine Leak Test:
- For detecting very small leaks using a tracer gas (helium) under vacuum or pressure.
- Gross Leak Test:
- For identifying larger leaks, often using liquids (e.g., fluorocarbon liquids) or bubble detection methods.
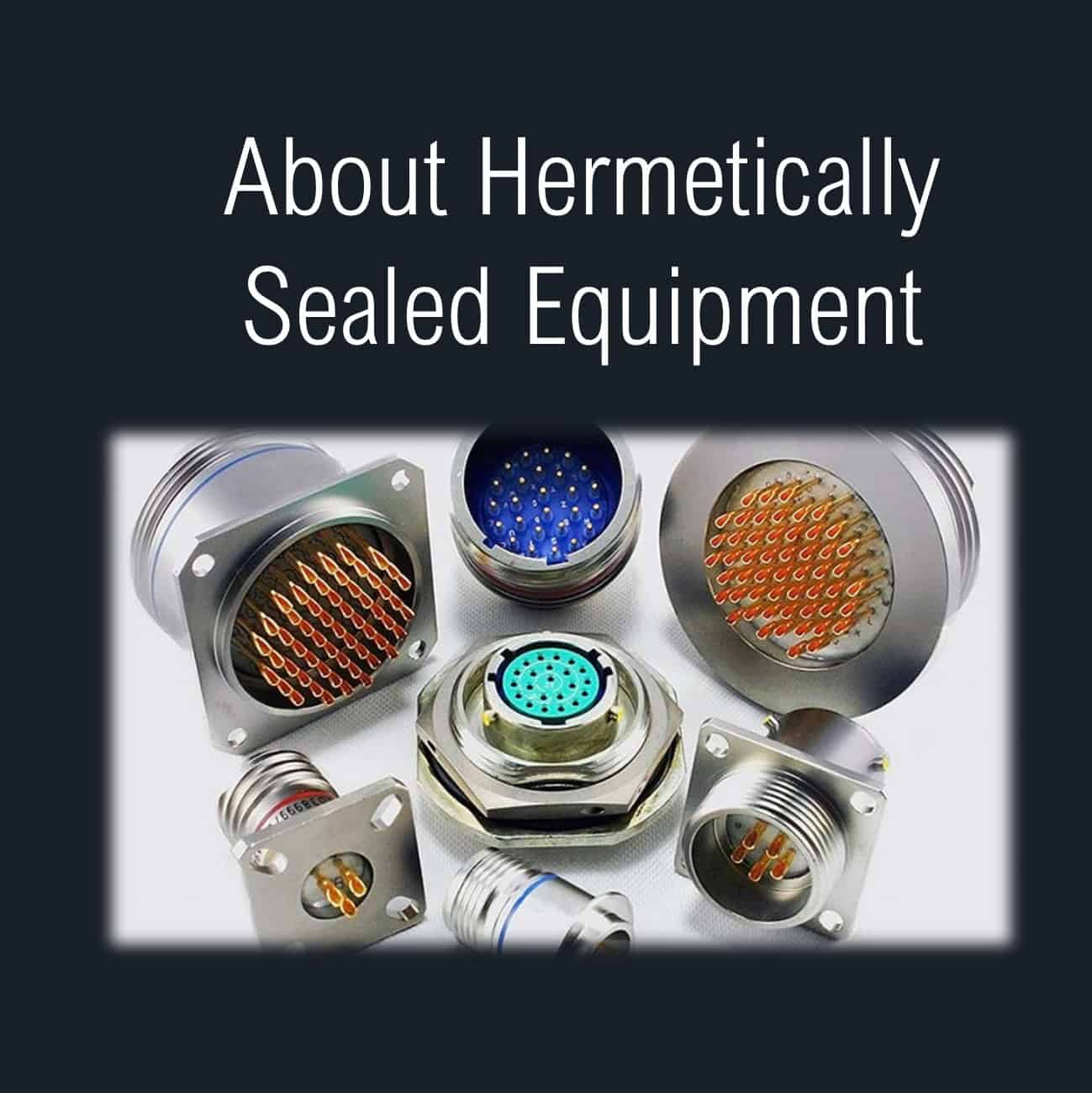