March 14 @ 8:30 am – March 16 @ 4:30 pm
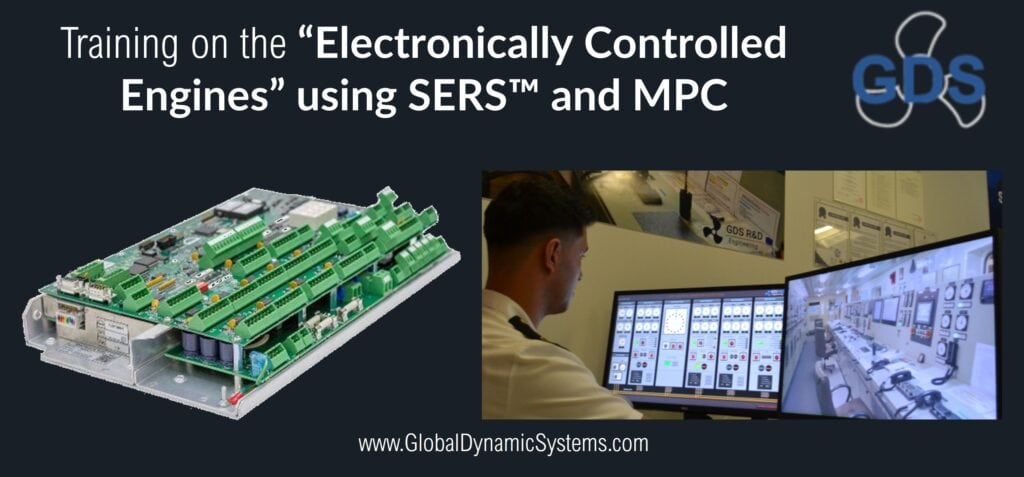
This training is for operational understanding and hands on applications for the Electronically Controlled Engines used as a main propulsion ship engine. It is an Online Training for the operation and management of ME type engine control systems with the use of a Multi Purpose Controller (MPC) and an Engine Room Simulator with ME type engine.
Who Should Attend this Training?
Marine Engineers working onboard ships of shore technical personnel as follows:
- Engineering officers working onboard ships: Chief Engineer, 2nd Engineer and watchkeeping offices
- Electrotechnical/Electric Officers
- Shore-personnel: Personnel working on the technical management side of the ship operating companies. Technical managers, inspectors, and superintendents.
3 days of hands-on ONLINE training using Ship Engine Room Simulator (SERS™) and a Multi-Purpose Controller (MPC)
- Day 1: Basic Operations with Engine Room Simulator (w/ME engine)
- Day 2: Advanced Operations with Engine Room Simulator (w/ME engine)
- Day 3: Electronically Controlled Engine – Operations and Maintenance
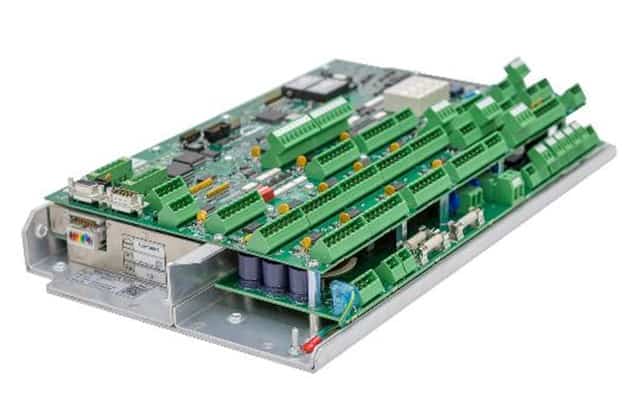
Electronically controlled marine diesel engines were designed especially in the 2000s in order to meet the requirements of MARPOL Annex VI to reduce ship-borne air pollution and ensure energy efficiency. With the development of the working conditions of traditional marine diesel engines, the training of responsible shift engineers has become an important need.
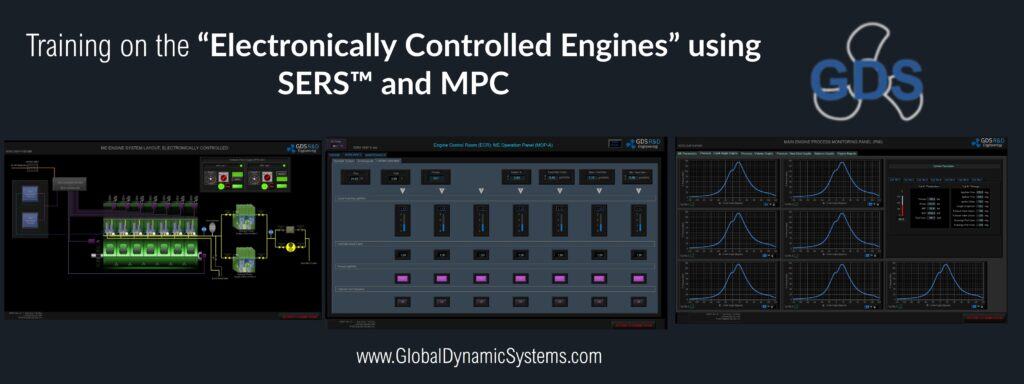
Minimization of human error and minimization of risks will be through familiarity with the failure scenarios to be experienced. In this sense, SERS™ engine room simulator training will be an important opportunity to prevent accidents resulting in material and life losses for ship personnel and companies with various scenarios such as possible malfunctions, routine operations and emergency scenarios.
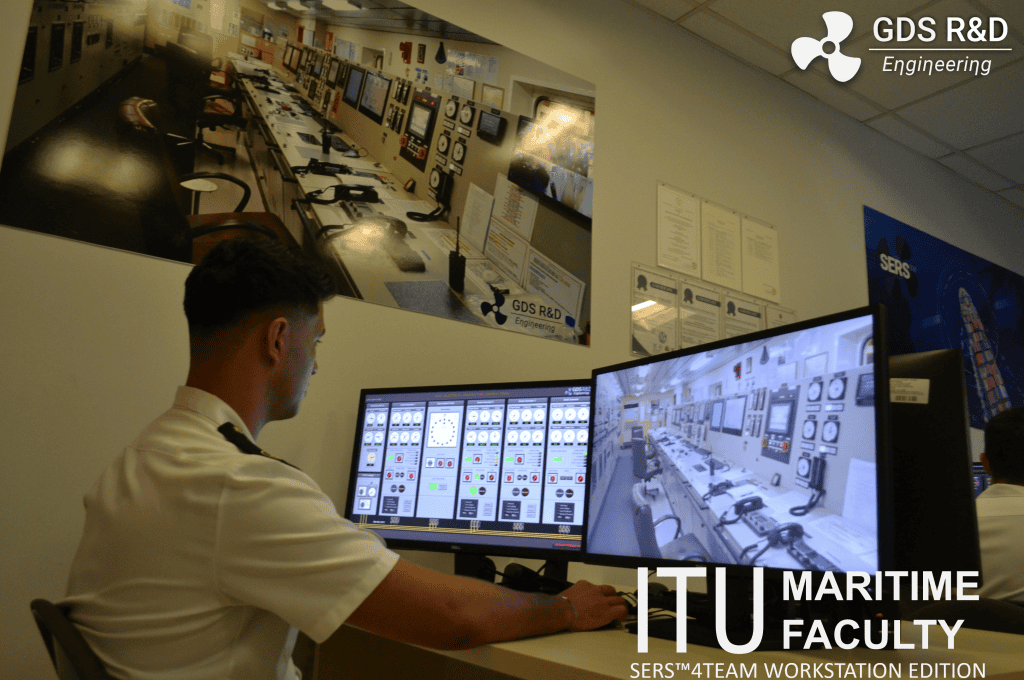
With the training designed as Basic Level (2 days) and Advanced Level (1 day), it is aimed to provide important information on topics such as the operation of electronically controlled marine diesel engines, possible malfunctions, and performance analysis. GDS Engineering R&D Team of Marine Engineering Training Experts has provided a solution to this training need, which is increasing day by day in global maritime trade, and aimed to increase the training efficiency by strengthening this solution with simulator and MPC applications.
Electronically controlled marine diesel engines is designed to reduce ship-borne air pollution and provide energy efficiency, especially in the 2000s to meet MARPOL Annex VI requirements. The training of responsible duty engineers has become an important need with the development of working conditions of commercial marine diesel engines,
Minimizing human error and minimizing risks will be achieved through familiarity with possible failure scenarios. In this sense, SERSTM engine room simulator training provides familiarity with endless scenarios and possible failures. In this way, it will be an important opportunity to prevent accidents that result in material and life losses for seafarers and companies due to failures. SERS™ provides full software functions for ME Controlled Engines that are currently in use onboard cargo ships. These tools are PMI, MOP A and MOP B panels, and additional engine performance diagram tools for monitoring and plotting the engine variables versus time or versus each other (X-Y graphs). The toold provide a mean of comparing the simulated variables against the actual ones recorded during actual tests, i.e. in factory or seakeeping tests.
The training, designed as basic level (2 days) and advanced level (1 day), aims to provide important information on electronically controlled marine diesel engines. GDS R&D Engineering aims to provide a solution for an important need in global maritime trade.
Training Program
Day 1
- Introduction: Development of Diesel Engines, Electronically Controlled Machinary and Engines, Differences between Electronically Controlled and Classical Diesel Engines
- Electronically Controlled Diesel Engine Structure and Components
- Hydraulic Elements
- Hydraulically Controlled Units and Panels
- Fuel system structure and elements
- Cylinder Lubrication System and Elements
- Exhaust Valve System and Elements
- Tacho Sistem
- Engine Control Systems
- Troubleshooting methods
- The most common malfunctions
- Service Notes/ Bulletins/ Circular reviews
Day 2
- Multi Purpose Controller
- Multi Purpose Controller Problems
- Performance Diagrams and Evaluations
- Simulator Application Sessions – Hands on Training using the Ship Engine Room Simulator (SERS™)
Day 3
- Advanced electronic elements and automatic control principles
- Advanced mechatronics and automation principles
- Multi Purpose Controller and a detailed discussion session
- FIVA Valve, Tacho, MCU systems – advanced level troubleshooting
- CoCOS-EDS, PMI
- Perofrmance calculations and evaluation with engine performance curves
- Simulator Application Sessions – Hands on Training using the Ship Engine Room Simulator (SERS™)
Training Method:
Face to face / Online
Training Material:
GDS SERSTM Engine Room Simulator / Multi Purpose Controller (MPC) application.
Training Cost:
Please get in touch with us for your training requests. The training is provided to indivuals and to organizations with groups.
Instructors:Two instructors provide the training.
This training will be provided by two instructors. One instructor has both academic and Chief Engineering experience with ME engines. The second instructor is a marine engineer with both sea experience and sngine room simulator instructor experience.
Enrollment Form
Enroll and reserve your seat today! Advance registrations of 1 month or earlier from the training date will receive a 10% discount!