MIL-STD-810H, US DOD Test Standard, starts with a meaningful phrase at the beginning paragraph of each of the 29 test methods: “Tailoring is Essential.” Understanding what this means and how to tailor the test methods for specific equipment’s specific platform applications is crucial, considering the platform, mission, and environmental requirements.
Develop Your Test Plan Early!
MIL-STD-810H is a huge guide for testing military equipment for military platforms. This means the described tests must be tailored to fit into your equipment’s intended functions and for the targeted platform use. For this reason, tailoring is essential for developing a test plan for 810 testing. And therefore, developing a test plan for testing of your equipment per MIL-STD-810H may take between 1 month to 6 months, easily. We strongly recommend that you don’t wait until the end of the development phase to complete your test plan. Rather, the test plan must be developed as early as possible, in the initial stage of the project, even before design-level efforts start.
There several reasons of completing a test plan early, some of these are:
- The specific tests to perform affect your design. Designers must know the test parameters when selecting solutions, such as test type, procedure, limits, and durations.
- A test plan should be completed and used for presenting it to the customer and stakeholders. Early agreements on the tests help identify your design limits early.
For developing a MIL-STD-810 environmental qualification test plan, following specific studies must be done:
- Selection of test methods and rationale
- Selection of procedures and test type
- Equipment to use
- Identifying the test limits and durations
- Developing a detail test procedures and associated forms
We study the Operational Requirements and Life Cycle Environmental Profile for your equipment and develop test requirements. If a Concepts of Operations (CONOPS) document does not exist, we create one or use the available information to establish an operational requirements document. With this study, the tests selected, methods, procedures, and envelopes to use become specific for testing your equipment. Unlike other test plans, developing a test plan for MIL-STD-810 testing may take 1 to 6 months.
For your military equipment, we develop test requirements, environmental test plans and test reports, with a research and study with the followin order:
We first develop test requirements by identifying
- equipment characteristics, functions, modes, and other specifics
- platform requirements
- applicable equipment specs
- equipment’s installation zone in the platform
- relevant rules and regulations
- relevant test standards
- other applicable standards
- test tailoring considerations: Environmental and Mission Profiles
And develop TEST REQUIREMENTS
- Just so you know, the test requirements may include tests from other standards. For example, Fire Flammability testing may be required for your equipment, which is not included in MIL-STD-810.
- Test requirements are list of the requirement statements and rationale.
Then, we develop Test Plan accordingly. When test plan is complete, that is when the test budget could be recommended.
Tailoring Considerations
A Generalized Task Statement for Tailoring: Consider the environmental effects. An example list is provided below. Develop exposure curves considering exposure scenarios. Use/develop a CONOPS document and generate a Life Cycle Environmental Profile (LCEP) for this.
- Environmental effects (temperature, humidity, icing, etc.) on the equipment in different operational modes: transportation, operation, and stand-by. Consider these effects with scenarios and develop exposure curves.
- Equipment vulnarabilities under the environmental/operational conditions.
- Effects caused by the platform operations (vibrations, shock, etc.)
- The effect due to the platform environment; various conditions in the section the equipment will be operating. For example, the equipment might be exposed to fluid contamination in the section where it will be installed.
- Equipment’s effect to the environment and systems (EMI, vibrations, fluid contamination, fire and flammability, etc.)
- Consider risks of operational breakdowns with “what if” scenarios.
How does the Life Cycle Environmental Profile (LCEP) affect the test procedures?
- LCEP should be developed for selecting the levels and durations of environmental tests, especially those that include climatic data.
- For each test method, each state or mode, such as transportation, operation, and storage, should be considered. Transportation can be either logistics or tactical transportation. For example, suppose military equipment will be transported by commercial aircraft. In that case, the vibration test should use the commercial aircraft’s vibration spectrum. In contrast, if the equipment will be transported by a military vehicle in the field, the transportation should consider the vibration spectrum of that vehicle.
- Equipment that is directly exposed to the external environment should consider the meteorological data provided in MIL-STD-810H Part I and Part III as well as MIL-STD-310 and AECTPs.
- Equipment that is not directly exposed to external environment should consider internal conditions, considering the maximum levels and duration of exposure.
How does Mission Profile affect the test procedures?
- Equipment’s modes and the durations to exposures could only be identified with clearly specifying the mission profile for the equipment.
Your equipment, for example, could be a device that must demonstrate the fire resistance. In that case, it is important to understand the aircraft fire zones and applicable procedures. For this, we not only review the test standard but also FAA/EASA documents to fully understand the described requirements and specs to develop a test case and procedure.
Risk analysis is another consideration.
- The results are not always pass or fail. We perform risk analysis to demonstrate and recommend alternate methods to pass if the result is negligible. We recommend design changes based on similar equipment tests or results for items that do not pass the tests. MIL-STD-882 provides the basic methodology for implementing risk analysis for this purpose.
Contents of an Environmental Qualification Test Plan
Systems engineering personnel appointed to develop a test plan must include the considerations explained in the paragraphs above. A test plan should be formatted such that it should generally include the following areas:
- Purpose statement.
- An introduction providing scope and background.
- A description of the test article, its components, and how it operates.
- A description of test requirements, including information for any deviation from this
document due to the applicability of the requirements. - Test setup, functional performance procedures, support equipment and facilities to be used.
- Specific safety concerns that the test article may pose during the tests along with risk
mitigation plans in accordance with (IAW) organizational safety policies and procedures. - Any planned on-ground or in-flight form, fit, and function checks.
- Performance or physical susceptibility criteria.
- List of reports to be generated.
- A test schedule.
- Referenced documents.
Phases of an Environmental Qualification Test Project
Additionally, if the project includes phases of the test and evaluation process, they should be included in a separate section, which may be called “Test Process and Phases.” For example, a test project may be divided into three section:
- Planning Stage: Plan to aim to complete the test plan early!
- Baseline/Performance Assessment: The baseline assessment also helps the personnel familiarize themselves with the equipment and prepare a test plan and forms while executing the tests.
- Verification of the key performance parameters to measure with tolerances
- Perform Quick Evaluations – no need to proceed if specific criteria are not met!
- If this step is performed with an expert team (Integrated Product Team) and users or user representatives, many potential issues can be solved before starting the physical tests, which can save time, effort, and money.
- Ensure the configuration of the item in its actual platform is defined with limitations.
- Quickly evaluate the equipment for the test methods, i.e., acceleration, vibration, contamination by fluids, temperature, solar radiation, etc. In many projects, we have identified issues that would happen during the tests.
- Identify the human interface items. Those items must be assessed, i.e., per MIL-STD-1472 Human Factor Assessment.
- Review the design and ensure that additional test standards are included due to the equipment’s design specifics, i.e., equipment with textile should be evaluated with other mil specs (type “textile” in Assist quick search tool). Although it is a colossal test standard/guide, MIL-STD-810H does not include many tests that may be required based on the equipment’s specific mission and its design specifics. Another example is that equipment must be tested for fire flammability, which is not included in MIL-STD-810H. These examples can be increased to being too many!
- Test Phase: The test plan should include the test method, standards to use, a summary of specific procedures tailored to its mission and Life Cycle Environmental Profile (LCEP), test criteria for each test method, test locations, and approximate test schedule. All lab tests are considered verification tests as per the systems engineering processes.
- Validation Tests: Any ground or flight, road, or seakeeping tests implemented with the user’s involvement in the operational environment.
- Reporting: Test results must be evaluated for risks and limitations. A risk assessment may be accommodated for any unexpected test results using MIL-STD-882. The test report must include
GDS MIL-STD-810H Training (Online or Onsite)
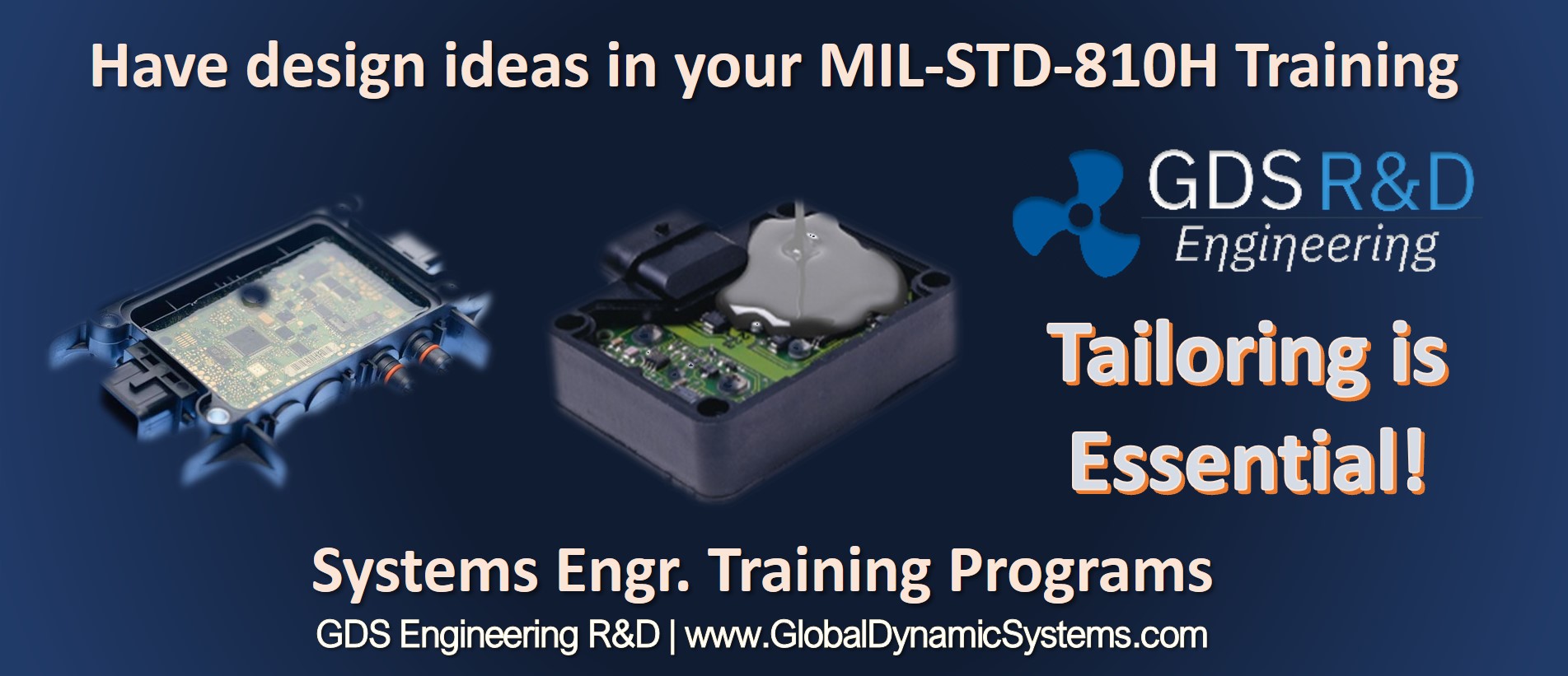
Our team has experienced test managers, Certified Verification Engineers (CVEs), and subject matter experts. If not, we will propose the appropriate team, but we will fully manage the project. In our team, Dr. Ismail Cicek worked in several test locations in the USA and Turkey and is still managing a test facility called the Marine Equipment Test Center (METC) in Tuzla, Istanbul. He has completed over fifty test projects in the USA test labs where he worked and is now more in numbers at METC and the METC personnel.
Why should you take MIL-STD-810H training from Dr Ismail Cicek and his team?
GDS Engineering R&D provides MIL-STD-810H training online or onsite. Performing operations in various parts of the world, we have provided this course to defense industry strategists, leaders, program managers, project managers, designers, and test engineers for over 15 years. With a lengthy background in test projects for DoD platforms, Dr. Cicek, the principal lecturer for this training, explains the tailoring process and concepts with specific application examples.
This course provides information and knowledge of experience on how to develop Concepts of Operations (CONOPS) document and Lice Cycle Environmental Profile (LCEP) to derive operational, therefore, test requirements for the Equipment Under Test (EUT). Understanding the tailoring part of MIL-STD-810H is the most important aspect of this test standard training for the following reasons:
- Although labeled as a “standard,” MIL-STD-810H is a “guide.” Therefore, MIL-STD-810 is a standard that is close to a GUIDE, whereas most other standards are close to a SPECIFICATION.
- Developing a test plan for MIL-STD-810H equipment testing might be confusing and time-consuming. Understanding the tailoring process helps you narrow down your test requirements rather than just following a standard.
- Training will explain why and when the CONOPS document is needed and how test requirements are established. It will also give a good knowledge of the EUT’s Mission and Environmental profiles. These are all covered by presentations and specific product examples discussed during the training sessions.
- In test method discussions, the instructor discusses “what items” (i.e., test levels) and “how” they will be tailored with specific examples.
Test methods, such as temperature, humidity, and temperature shock, require the establishment of mission and environmental profiles to successfully determine the test levels, durations, and pass or fail criteria.
GDS Engineering R&D, Inc. is a leading provider of MIL-STD-810H training, offering comprehensive courses designed to equip professionals with the knowledge and skills necessary to navigate the complexities of this crucial military standard. MIL-STD-810H focuses on environmental qualification testing for military platforms and defense equipment, ensuring reliability, durability, and successful product development. Our courses cover a wide range of topics, from fundamental concepts to advanced techniques, including shock, vibration, temperature, humidity, altitude, salt fog, dust, rain, fungus, acceleration, transportation, and operational testing.
A key aspect of our MIL-STD-810H training is the emphasis on Tailoring Methodology for MIL-STD-810. Participants learn how to effectively apply tailoring techniques to develop accurate Life Cycle Environmental Profiles (LCEP) and Mission Profiles for specific equipment and operational scenarios. This ensures that testing is relevant, efficient, and cost-effective. We offer various training on MIL-STD-810H, including MIL-STD-810H training course for engineers, MIL-STD-810H certification online, and hands-on MIL-STD-810H testing workshops. These programs cover the latest revisions to MIL-STD-810H and provide practical guidance on environmental test management, including environmental test sequence development and execution.
GDS Engineering R&D, Inc. provides flexible training options to accommodate diverse needs. Our online training programs offer convenience and accessibility, while our international training programs cater to a global audience. We also provide specialized training, such as the Systems Engineering Training Program, which integrates environmental considerations into the systems engineering process. Our courses are instructor-led, with opportunities for hands-on learning in our accredited lab. We are committed to providing high-quality training that empowers professionals to effectively address environmental effects and environmental considerations throughout the lifecycle of defense equipment.
In response to the challenges posed by COVID-19, GDS Engineering R&D, Inc. has implemented measures to ensure the safety and well-being of our participants. We offer virtual training options and have adapted in-person training to adhere to social distancing guidelines. Our commitment to providing valuable and accessible MIL-STD-810H training remains unwavering, even amidst these challenging times.
Please read more information on our MIL-STD-810H Training pages.
Additional Links for More Reading:
Tailoring is Essential: Our dedicated page describes more about tailoring.
Training on MIL-STD-810H Testing: Our online training details are provided. A good training helps your personnel develop better test plans and save time, effort, and money at the project completion.
Check out our calendar for training programs: GDS Training Calendar.
Systems Engineering training courses provided by GDS Engineering R&D, including MIL-STD-810H, RTCA-DO-160G, MIL-STD-461G, Requirements Management, MIL-STD-704F, and EMI/EMC General Training. Information is provided on this page.